Shifting a Paradigm with Complex Stakeholders
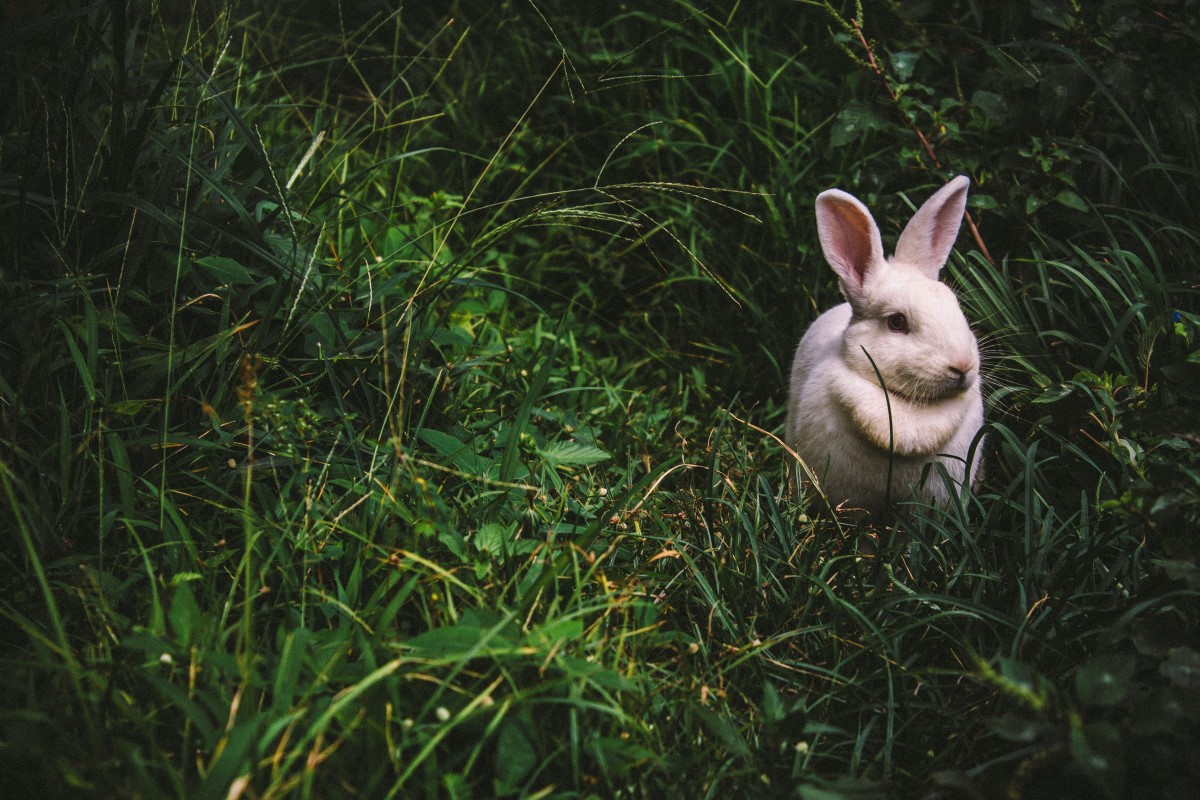
Summary
In this change diary, you will learn about the importance of change management in the field of biomedical research. Read on to learn more about a coming paradigm shift, will be characterised by the so called 3Rs principle: reducing, replacing and refining, as it relates to the use of animals in research.
Learn how a major global pharmaceutical company applied good change management practices to guide the people shift required to adapt to a significant, industry wide change, which was to affect at least 3000 people in their organisation. Laura Viviani, our newest Partner from Basel in Switzerland, relates her experience as the Project and Change manager of this fascinating engagement.
Background
Biomedical research is experiencing times of significant, fundamental change, as the use of animals in the some part of its research process is being questioned both scientifically and ethically. On one hand, parts of the scientific community are calling for a shift away from animal-based research and experiments to alternative methods. On the other, there is also significant societal pressure to stop the use of laboratory animals, and improve the ethical standards regulating their use. Although predominant in the west, this theme is spreading and receiving ever growing support. There is a paradigm shift coming, characterised by the so called 3Rs principle: reducing, replacing and refining, as it relates to the use of animals.
Pharmaceutical drugs/vaccine manufacturers are on the receiving end of a complex set of demands, enmeshed in a variety of ‘gravitational fields’ that pull them both towards the 3Rs and away from them. The potential cost savings and increased quality promised by 3Rs clashes with the imperative to not disrupt internal processes/production. Internal support for replacement of animals and their improved welfare is usually much less powerful than the subtle resistance of clinging to established procedures/habits, and management unwillingness for what is effectively a risky transition. Strong societal pressure may push for quick change, but regulators – who have the final word in decisions about drug and vaccine production – are extremely risk averse and securing their support for a proposed change requires large investments in time and resources, with the final outcome uncertain.
Yet the shift is inevitable: the move away from animal use is not a matter of if, but rather a matter of when. The key difficulty is obviously: how do you make the transition?
As one of the top global vaccine manufacturers, we certainly faced this challenge. And the realisation that other manufacturers had taken the lead finally spurred us into action. Thus, after considerable discourse and analysis of the potential drawbacks, frictions and even disruptions that it might cause, we decided to embrace the change globally, and made it a priority with all the resources to achieve it. Despite the enormity of the transition and all these pitfalls and difficulties, rather than resisting the tide, the company decided to embrace the shift and be at its forefront.
The benefits were apparent: proper implementation would reduce costs by eliminating laboratory animals (even if partially), which are expensive to purchase and to care for; improve ethical standards by eliminating animal welfare issues, and ultimately increase the overall quality and safety of products as growing scientific evidence disfavours animal testing as a precise instrument for quality/safety evaluation. Accordingly, despite the gargantuan scale of the transformation that was clear from the beginning, the decision was taken to foster the establishment of a new internal mindset/culture; review/transform processes affecting vaccine creation and production and help the company transition away, as much as possible, from animal-based testing to alternative methods.
The Challenge
Changing techniques and procedures across sites in Europe, US and Asia made this an extremely complicated transformation. Vaccines are highly complex biological substances administered to healthy people (including infants) and animals, and their safety is understandably paramount. Every production step is tightly and rigidly regulated, and authorities tend to frown at proposed changes in production/testing methods, unless they can be exhaustively proved not to lower overall safety. Implementing the 3Rs would thus constitute a significant transformation and need close scrutiny by the authorities.
By law every change in method needs to be submitted to authorities for evaluation, and can be adopted only after their approval. But you can never take this approval (and the time required to get it) for granted.
From an organisational perspective, the operational challenges included:
- Vaccines are produced in different countries for export to a variety of markets. Regulatory harmonisation is low, and manufacturers are forced to comply with a long series of market-specific safety requirements. Any change is very burdensome, as different regulators in different countries must all be satisfied.
- Drivers for producers and regulators differ: while they both consider safety as pivotal, producers are interested in marketing new products, increasing efficiencies and lowering costs, while regulatory authorities are safety-driven with a conservative outlook on innovation rooted in absolute prudence, which often makes them overly sceptical;
Impact on People
Due to the scale and complexity of the change, a total of approximately 3,000 employees were expected to be directly affected by the change: from general management to senior and mid-level managers, all the way down to shop-floor. This would include staff in all functional areas, including R&D, Quality, Production, Supply Chain and Animal Facility Teams. A change of this scale was expected to impact the culture within the organisation, and therefore some of the focus of the change management would need to be upon ensuring an openness to ongoing engagement and the ability to overcome any anticipated fears.
Ten percent of people were expected to become redundant, although as many as possible would be reassigned rather than dismissed. The needed influx of new scientific and technical expertise was addressed in the short/mid-term through training of existing personnel, recruiting new hires and employing external consultants.
Regulatory Impact
The majority of regulators’ worldwide a priori tenet can be summarised as ‘current methods are to be considered safer than newer ones, in the interest of collective security.’ The corollary is that only the results of those methods are accepted by regulators as proofs of safety. Therein lies the challenge: different test methods, not relying on animals, cannot produce the same kind of data as that produced by animals. The problem is thus ontological and can only be solved when there is mutual trust and openness to new methods.
But the understandable institutionalised coldness toward the new approach of many regulators, emerging from the need to protect the public, has the unintended consequence of stifling efforts to innovate and discouraging manufacturers. Some initiatives and decisions toward the use and implementation of 3Rs coming from some regulators, gave to the company another supportive arguments for the transformation that was chosen, as it was clearly going to impact the very pillars of its business. Therefore, gauging the consequences, and foreseeing and anticipating the difficulties and the external opportunities to leverage for the transitioning to the 3Rs principle was paramount.
Other Considerations
The desired change was further complicated by the fact there was no clear finishing line. The program would not end with a “we are finally there” moment, as the science to fully eliminate animals still does not exist: much is possible, a lot is advisable, but the target will be moving for years to come as the science involved is in constant flux.
The company’s technical and scientific perspectives would need to be transformed, internal values re-geared, and these transformations enacted with the awareness that the company had committed to a philosophy rather than to an objective. To this end, special guidance and strong engagement would be key, as the absence of a defined endpoint could amplify the consequences of drawbacks and stifle the energy towards change. In the light of this complexity, the program’s minimum time span would be at least ten years.
The Approach
As both the project and the change manager, I sat in between the sponsor, to whom I reported; and senior- level management, with whom I was in direct collaboration; and facilitators in the various offices, who reported to me. Our initial focus was on the planning (and ultimate execution) of a series of activities to preliminarily map all the information that could be useful in the program, including:
- Mapping stakeholders
- Reviewing animal-based activities throughout the entire the organisation
- Identifying the change opportunities (where to implement 3Rs)
- Engaging in a series of 1:1 dialogues to outline the prevailing internal culture and attitude towards the issue, gauge interest/resistance to the change, and understand what each stakeholder would need to implement the change (knowledge, resources, decision making, creation of new processes, etc.)
The general strategy to execute the program revolved around three key activities:
Continuous feedback was collected from the various projects (difficulties and successes met, needs arisen, lessons learnt etc.) to keep the pulse of the ongoing transformation, and efforts were made to keep the program under the spotlight by continually celebrating successes. To prevent resistance to change, a ‘speak-up’ attitude towards setbacks was encouraged.
Implementation activities were clearly focused on engaging the stakeholders and included:
- 1:1 meetings wherever possible, with management, scientists and other employees
- constant communication and reporting activities, direct and synthetic in form so as not to require excessive time for its consumption
- workshops/events on the different change projects and on the overarching global program where held in most of the sites, to secure a feeling of inclusion
- CM objectives were included in the personal objectives of every stakeholder at every level, which drove awareness of the importance of every person in the change process (this certainly helped to drive engagement)
- Providing the main sponsor with high-level monthly reports to ensure her engagement, and offer success stories to use for the internal high management communication
Lastly, micro-management was foregone in favour of a transfer of responsibilities to specific group members as a way to further personal commitment, and the various projects were tailored on the styles and needs of the people in the relevant workstream.
In my opinion, those last three lines hold a large part of the program’s success.
Of course, the scale and depth of the programme (transforming key processes and attitudes in geographically and culturally distinct sites) made the CM process remarkably fluid: both strategy and the specific plans underwent continuous refinement, and at times significant redefinition was needed as result of the organizational response. Fortunately, the entire process benefitted from a relatively stability environment (in terms of changes in leadership) for approximately 4 years.
6 Years Later
Six years later, the programme is still well under way, and its importance firmly established. The internal philosophy and values it promoted have been embedded into all the key decision making internal committees, and it has changed Standard Operation Procedures and various processes in research, development, production and quality testing. In general, it has become part of the very mindset of the organisation. Further proof of this is the fact that change now comes spontaneously from inside the company, with parts of the organisation proactively kick-starting their own proposals. At a global level, the change has been absorbed and internalised and the company as a whole is an active member an international partnership on alternative methods to animal testing and the promotion of global harmonisation of regulatory requirements.
There is still much to be done, but the results have already informed the company’s present, and will certainly shape its future.